What is a CAPA, and Why is it crucial to your Medical Device development?
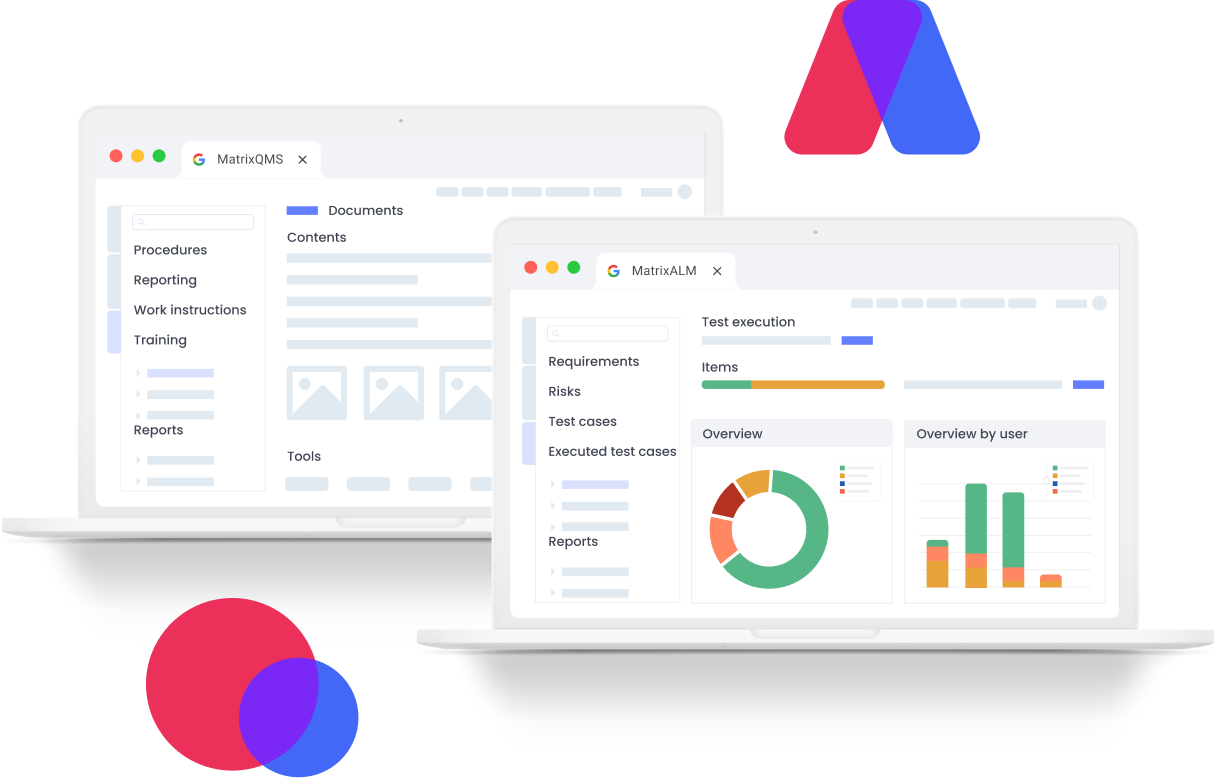
What is a CAPA, and why is it crucial?
Guaranteeing the quality and safety of a product is the key to success for any business. For medical device development, where precision and safety are crucial, CAPA is essential.
We all understand the importance of quickly investigating and eliminating issues relating to the development of medical devices. Prompt responses to such issues will help avoid adverse consequences, not only in the form of non-compliance with government regulations and user requirements but also even harm to users or patients.
User complaints, failure during testing, audits and manufacturing errors are just a few examples of where CAPA comes into play.
Let's take a closer look.
What does CAPA stand for?
CAPA is the shortening of corrective and preventive actions. CAPA is a mandatory part of the Quality Management System (QMS) for any medical device manufacturer under the U.S. Food and Drug Administration (FDA). CAPA is also an integrated part of ISO 13485. We explained what ISO 13485 is and who it is used by.
CAPA definition
According to a regulatory definition, corrective action is an action to eliminate the cause of a detected nonconformity or other undesirable situation.
Here important to note that the definition of corrective actions is often mixed with correction when talking about CAPA. Correction is an action to eliminate the detected nonconformity itself, and not the cause of this nonconformity. A correction can be made in conjunction with a corrective action and should not be considered as an alternative.
Preventive action is an action to eliminate the cause of a potential nonconformity or other undesirable potential situation.
When it comes to the CAPA meaning in general we refer it to as a systematic approach to identifying and fixing issues that have been detected and preventing potential issues from happening.
What Is the Difference between Preventive Action, Corrective Action and Correction?
Preventive actions are measures taken proactively to avoid the occurrence of a problem. The aim is to anticipate and mitigate potential issues before they arise.
Correction should be considered as immediate actions taken to address a problem in real time with a focus on containment and resolving the immediate impact of the issue.
Once corrections are done, corrective actions come in that go beyond immediate fixes, targeting the underlying issues for long-term resolution.
How does this work in real life?
Imagine a company that makes digital thermometers to monitor patients' temperatures. During routine testing, a company discovers that a certain batch of thermometers are producing inaccurate readings, which can lead to potentially misdiagnoses in clinical settings.
To prevent this problem from occurring (preventive actions), a company:
- implements additional quality checks during production
- introduces more stringent calibration procedures, and
- provides additional training to the production team to ensure accurate temperature readings in subsequent batches.
If the problem was identified with inaccurate thermometers already on the market, a company first takes correction and recalls the products of the corresponding batch. This fix resolves a pressing issue for users who have already purchased defective devices.
To prevent similar inaccuracies from reoccurring in the future (corrective actions), a company will
- conduct a thorough investigation,
- identify the specific component of the defective lot that was not properly calibrated,
- revise the calibration process,
- conduct additional inspections of critical components, and
- further train the quality control team to ensure the conformity of future batches accuracy standards.
What we can learn from the example is that the preventive actions prevent the occurrence the problem, correction is to containment while corrective actions prevent the same problem from recurring in the future.
Why it is important to use CAPA?
Quality standards require the medical device industry to have a CAPA process in place. But it's not just about following rules.
CAPA provide companies with a step-by-step approach to dealing with non-conformities. The CAPA helps companies identify nonconformity issues that negatively impact the quality of a product or a process, fix these issues through targeted action, and stop new ones before they happen.
An integrated CAPA process in a quality management system lets companies go beyond just documentation to take action that improves the overall quality and reduces the risk of non-conformance.
5 phases of effective CAPA
Continuous improvement and enhanced product and process understanding can be achieved using a well-established CAPA process. Various guides and frameworks have been developed to describe the CAPA process. We stick with 5 phase framework considering that each of these phases can be further expanded on.
Identification
A clearly defined quality issue or nonconformity incident (altogether as a problem) is essential for the later work and the effectiveness of the CAPA process. The initial phase of the CAPA process is to describe, document a problem and determine if it warrants a further investigation.
Events triggering CAPA can occur from various sources, both internal and external.
But remember that not all problems automatically equal CAPA.
Back to the digital thermometer manufacturing example, a temporary disruption in the supply chain of a minor component (say due to weather conditions) does not have a significant impact on the functionality or quality of the final product. This problem can be resolved without requiring a formal CAPA process because it is considered a routine operational problem with no indication of a recurring problem.
The goal of this phase is to ensure that all relevant information about the problem is collected so that appropriate next steps can be taken. This data may help to identify the root cause of the problem and further actions that could be taken to prevent it from happening again.
During this phase, a product or process affected by incidents, issue description, and first-date occurrence should be defined properly. Even if the problem is rejected as a CAPA, be sure to document the reasoning and enact any corrections. That may be needed to monitor for future incidents.
Evaluation
The problem is required to be evaluated in terms of the potential impact, for instance concerning safety, reliability, costs, customer satisfaction, quality audit reports, quality records, service records, complaints, and returned products.
A risk assessment matrix can be used as a feasible tool for problem evaluation. This evaluation is used to decide the priority of the actions as well as the level of investigation.
Additionally, corrections might need to be implemented during this phase until the investigation is closed and corrective actions defined and implemented.
To be prepared for the further phase, be sure you do not fall into such pitfalls as confirming a problem understanding, accepting opinions as facts, or failing to record information.
Investigation
The third phase of the CAPA process is investigation. There are many root cause analysis tools and techniques to investigate a problem, namely
• 5 Why analysis
• Fishbone diagram (a.k.a. Ishikawa diagram)
• Failure mode and effects analysis (FMEA)
• Fault tree analysis (FTA)
• Pareto charts
• or even a combination of it can be used.
There are no strict requirements on how to approach the problem investigation but knowledge gained through the first two phases of the process should be considered.
Implementation
The implementation phase is all about applying preventive/corrective actions in practice. This involves following the planned steps to resolve the problem.
A clear assignment of responsibilities for each point of the plan will allow us to determine who is responsible for the implementation of corrective and preventive actions.
To ensure timely completion, the timeline for each action should be realistic. This will help track progress and prevent delays in completing planned actions.
Adequate resources are key to successful completion. Allocate the necessary resources, including personnel, materials, equipment, and budget, to support the implementation of the action plan.
If corrective or preventive actions introduce new procedures or processes, provide training to appropriate personnel. Ensure that employees have the knowledge and skills necessary to effectively implement the changes.
Communication is very important at this stage to ensure that all participants are aware of the changes and their roles in the process.
Verification
Having a CAPA program in place doesn’t guarantee its effectiveness by default.
To ensure that the decisions you made were the right ones and that no further risk was caused, the final CAPA phase is all about verifying the effectiveness of your CAPA process and follow-up.
There are two key points of this follow-up: verifying that all tasks have been carried out to completion and making sure they were effective.
It means ensuring that actions are effective and do not adversely affect the finished product or process. To do so you may need to ask questions like:
Did the action correct/prevent the problem(s)? Have all planned actions been implemented? Is there a chance that the actions have led to any additional adverse effects? Did the corrective/preventive actions indeed take away the problem?
Choosing the optimal CAPA software for your company
An effective CAPA process is essential for driving structured and measurable improvements, preventing issues, and ensuring compliance with regulatory requirements.
However, it’s important to note that the result of CAPA handling is only as good as the tool that is used to manage problems. For CAPA to be effective, businesses must have a robust system in place for collecting data and identifying trends.
At Matrix Requirements, the CAPA process has been integrated into MatrixQMS - an electronic quality management system (eQMS). This structured approach allows for a clear and one place to document the problems, conduct root cause analysis, assign responsibilities and timelines and develop and implement corrective and preventive actions with further follow-up. If you are curious about how a well-established CAPA process can contribute to quality improvements of your product, feel free to contact us for a demo.