Medical Device Product Realisation Documentation: A Comprehensive Guide
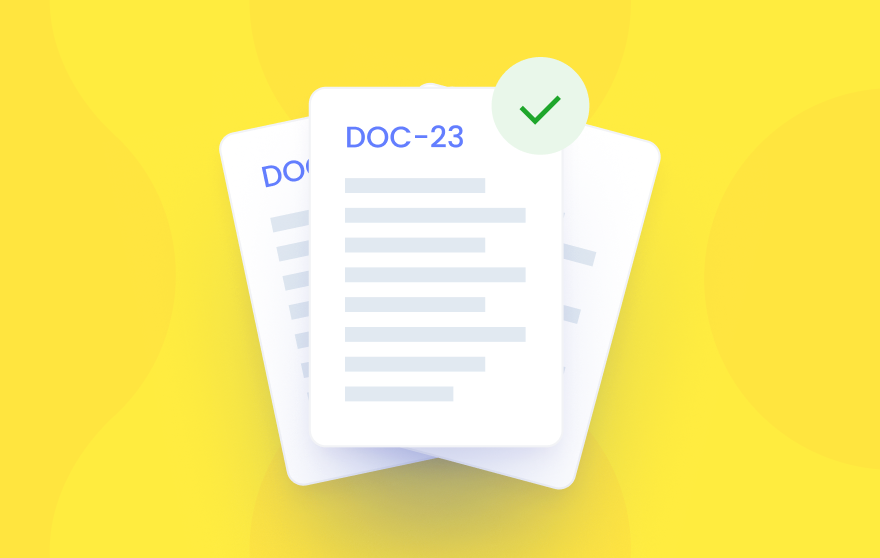
Effective medical device production hinges on rigorous documentation.
It's the backbone of the entire lifecycle. From conception to post-market surveillance, each phase of a medical device's journey necessitates comprehensive record-keeping that aligns with regulatory standards such as ISO 13485, MDR, and FDA requirements. Robust documentation is not just a regulatory hoop to jump through; it is foundational to ensuring quality, traceability, and patient safety. This process-centric approach empowers stakeholders to navigate the complexities of medical device product realization with confidence.
Understanding Product Realisation in Medical Devices
Medical device product realization is a systematic and structured journey, punctuated by meticulous documentation and adherence to stringent regulations. It involves a sequence of interrelated processes that, cumulatively, bring a medical device from concept to market. Essential to this journey is a robust framework outlined by ISO 13485 standards, the Medical Device Regulation (MDR), and U.S. Food and Drug Administration (FDA) guidelines. At each step, from design and development to production and post-market surveillance, specific documentation captures the lifecycle of the device, ensuring meticulous control and assessment. Utilising an item-based approach for documentation facilitates traceability and enhances the integrity of documentation, providing a transparent pathway through the product’s evolution.
Processes of product realisation
The product realisation process encompasses several key processes that are essential for the development and realization of a medical device. These processes include:
Design and Development Process: This process involves the creation and refinement of the device's design, taking into account user needs, regulatory requirements, and technical specifications.
Risk Management Process: The risk management process identifies, analyses, and mitigates potential risks associated with the device throughout its lifecycle. This includes conducting risk assessments, implementing risk controls, and monitoring the effectiveness of these controls.
Verification Process: The verification process ensures that the device meets specified requirements and performs as intended. This involves conducting objective tests, inspections, and analyses to confirm that the device meets design inputs and regulatory requirements.
Validation Process: The validation process demonstrates that the device, when used as intended, consistently produces the desired results and meets user needs. This typically involves conducting clinical evaluations, performance testing, and usability studies.
Production and Service Provision Process: This process involves the manufacturing, assembly, and packaging of the device, as well as the establishment of processes for its distribution, installation, and servicing.
Control of Monitoring and Measuring Equipment Process: This process ensures that the equipment used for monitoring and measuring the device's characteristics is properly calibrated, maintained, and controlled to ensure accurate and reliable measurements.
Control of Nonconforming Products Process: This process establishes procedures for identifying, documenting, and addressing nonconforming products or materials to prevent their unintended use or distribution.
Corrective and Preventive Actions Process: This process involves the identification, investigation, and implementation of actions to address nonconformities, prevent their recurrence, and continually improve the effectiveness of the quality management system. By effectively managing and documenting these processes, medical device developers can ensure compliance with regulatory requirements, mitigate risks, and produce safe and effective products.
Key Elements of ISO 13485 and MDR Compliance
Compliance with ISO 13485 and MDR is predicated on a systematic documentation strategy that aligns with regulatory demands.
Tight integration of all documentation is a bedrock for successful audits and sustained regulatory compliance in the medical device sector.
For medical device developers, establishing a quality management system (QMS) is pivotal, enhancing process effectiveness and meeting regulatory expectations.
Leveraging the item-based approach ensures that every piece of documentation is traceable and interrelated, forming a cohesive narrative of the device's lifecycle.
A Quality Management System (QMS) under ISO 13485 should cover the following process areas:
Management Responsibility: This includes establishing and communicating the organisation's quality policy, defining roles and responsibilities, and ensuring the availability of resources for the QMS.
Resource Management: This involves managing resources such as personnel, infrastructure, and work environment to support the effective operation of the QMS.
Product Realization: This encompasses the processes related to the design, development, production, and service provision of medical devices, ensuring compliance with regulatory requirements and meeting customer needs.
Measurement, Analysis, and Improvement: This includes processes for monitoring and measuring product and process performance, conducting internal audits, managing nonconformities, and implementing corrective and preventive actions.
Document Control: This process area focuses on establishing procedures for creating, reviewing, approving, and controlling documents and records related to the QMS.
Purchasing and Supplier Management: This involves processes for selecting, evaluating, and monitoring suppliers to ensure the quality and safety of purchased products and services.
Risk Management: This process area addresses the identification, assessment, and mitigation of risks associated with the design, development, production, and use of medical devices.
Regulatory Compliance: This includes processes for ensuring compliance with applicable regulatory requirements, such as obtaining necessary approvals and maintaining documentation to demonstrate conformity.
By covering these process areas within the QMS, organisations can establish a robust framework for quality management and compliance with ISO 13485 standards.
FDA Regulations Impacting Product Development
The FDA regulates medical devices through a set of stringent requirements to ensure public safety.
Quality System Regulation (21 CFR Part 820): This mandates manufacturers to establish and follow quality systems, which are comprehensive to cover all stages of product development.
Design Controls (21 CFR 820.30): Establishes a framework that medical device manufacturers must use during the design process to ensure that products meet user needs and intended uses.
Risk Management (ISO 14971): Although an ISO standard, it's integrated into FDA expectations to ensure a systematic approach to managing risks associated with medical devices.
Premarket Notification [510(k)] and Premarket Approval (PMA): Regulatory pathways for devices to receive FDA clearance or approval before being marketed.
Software Documentation: Requirements specified in FDA guidance for software, including software validation and maintenance activities.Understanding and adhering to these regulations is crucial for market access.Comprehensive documentation underpins FDA compliance, serving as evidence of a quality-centric development process.
Structuring the Documentation Process
When structuring the documentation process, establishing a methodical approach to manage and organize documentation is paramount. This involves creating a strategic map, which defines the flow of document creation, review, approval, and revision cycles. It is essential to interlink the various stages of documentation to maintain a cohesive and compliant record trail, underpinned by a robust document control system that ensures documents are current and retrievable.
The organization of documentation must consider an item-based methodology, where each information item serves as a fundamental building block in the documentation architecture. By linking related items—such as design requirements to risk assessments, or test cases to validation protocols—developers create a traceable and dynamic documentation system. In this system, real-time updates to one item cascade through associated documents, maintaining accurate record integrity that is essential for regulatory scrutiny and quality assurance throughout the product realization process.
Essential Documents for Medical Device Realisation
To ensure compliance with ISO 13485, MDR, and FDA regulations, a comprehensive suite of documents is integral throughout the entire medical device product realization process. These documents serve as a roadmap, guiding developers from the initial concept to post-market surveillance, while also ensuring traceability and meeting verification and validation requirements.
The product realisation process begins with the Design and Development Plan, which outlines the overall strategy and approach. This is followed by the creation of various documents, including Inputs, Outputs, Reviews, Verification, Validation, and Transfer records, which capture the necessary information at each stage of development.
For a seamless transition from concept to a market-ready product, it is crucial to have well-documented Product Requirements Specifications (PRS), Risk Management Files, and Clinical Evaluation Reports (CER). These documents not only demonstrate compliance with regulatory obligations but also serve as evidence during audits.
To achieve traceability and meet verification and validation requirements, it is essential to establish clear links between the documents and information sources. This includes the need for also linking requirements to risks, technical specifications, and user requirements. Using documents as information base, makes is almost impossible to trace how requirements are implemented and verified throughout the product realization process. Manually keeping track with lists of identifiable single requirements, specifications etc. is a hard challenge for developers and document managers and bears high risk of errors in each step.
By utilising an item-based approach, such as the one offered by Matrix Requirements with MatrixALM, developers can effectively manage and update their documentation. This approach allows for the cataloging of requirements, specifications, risk analyses, test cases, and more as discrete but interconnected information items, ensuring comprehensive traceability and facilitating compliance with standards and regulations.
By adopting this comprehensive approach to documentation and traceability, medical device software developers can enhance their oversight, control, and efficiency throughout the product realization process. This not only mitigates compliance risks but also expedites time to market, ultimately leading to the successful launch of safe and effective medical devices.
Implementing the Item-Based Documentation Approach
The item-based approach to documentation encapsulates discrete information units, each pertaining to specific aspects of product realization. These items are inherently designed to simplify traceability and ensure comprehensive coverage of all necessary data points.
In practice, each item represents a granule of data, whether it be a requirement, a risk assessment, testing protocol, or other crucial information. As a development process evolves, these items can dynamically interconnect, creating a robust framework that allows for real-time updates, changes, and enhancements without compromising the document's integrity or regulatory compliance.
By embracing this approach, developers facilitate a more efficient review and approval process. Since information items are version controlled and logged, each stakeholder can access up-to-date, context-specific data, which expedites decision-making and regulatory submissions. The visibility of the linkages between items demystifies how each piece fits within the larger product lifecycle.
Furthermore, tools such as Matrix Requirements showcase the practicality of this approach, integrating modules like MatrixQMS for quality management and MatrixALM for alignment with product realization processes. These cloud-based solutions foster a seamless generation of regulatory documents, such as Product Requirement Specifications, by compiling approved items. This not only improves accuracy in the documentation but also leverages the power of digital traceability to uphold the highest standards of quality and regulatory adherence.
Leveraging Matrix Requirements for Documentation
The genesis of a medical device begins with meticulous planning and documentation. Matrix Requirements' MatrixALM module provides an infrastructure to structure this process, allowing each phase's output to serve as the genesis for subsequent stages. By mapping out these connections, we establish a comprehensive and traceable documentation lineage that forms the bedrock of product realization.
Within this framework, Matrix Requirements adeptly manages various forms of data. Requirements, specifications, test cases, and more coalesce into a cohesive web of interlinked information items. Utilizing MatrixQMS, the workflow ensures each relational link mirrors the rigorous standards of ISO 13485, MDR, and FDA, offering a dependable skeleton for compliance and quality management.
Matrix Requirements embodies an 'item-based approach' where documentation is dynamic and alive. This cloud-based, scalable platform ensures that the artifact of today—the Product Requirement Specification, for instance—emerges seamlessly from a tapestry of stringently reviewed and approved items, inherently adaptable to the demands of regulatory landscapes.
Navigating MatrixQMS for Quality Management
MatrixQMS is an integral component for effective quality management workflow.
Document Control: Maintain a rigorous documentation trail, ensuring all versions are logged and accessible. Document templates that are pushed to the respective product lifecycle application ensure traceability of QM processes to their implementation.
Audit Management: Prepare and conduct audits with traceable records and clear audit trails. Use Review functionality to directly trace audit findings to process and documentation adoption.
Training Management: Keep track of staff training, qualifications, and certifications efficiently. Demonstrate qualification of responsible employees.
Supplier Management: Monitor supplier qualifications and performance for compliance. Manage suppliers linked to QM and product lifecycle documentation.
Non-Conformance & CAPA: Log and track non-conformance issues, and manage Corrective and Preventative Actions. Directly link from issues to risks, change requests, and the implementation of changes to validated release specifications.
Leveraging MatrixQMS enhances compliance with standards such as ISO 13485.
The platform streamlines quality management processes, offering full traceability and version control.
Utilizing MatrixALM for Product Lifecycle Management
MatrixALM excels in orchestrating the intricate details of medical device lifecycle management.
Requirements Management: Track every requirement from inception to delivery, ensuring full traceability.
Risk Management: Identify, assess, and mitigate risks, linking them directly to relevant requirements and controls.
Test Management: Effortlessly connect test cases to requirements and record results for comprehensive verification.
Issue and Change Management: Manage problem reports and change requests with a complete history of alterations and justifications.
Release Management: Oversee product releases with detailed release records, ensuring controlled and compliant distribution.
The modular interface of MatrixALM simplifies the complexity of medical device development.
Through seamless integration, MatrixALM ensures every process stage is transparent, managed, and compliant.
Ensuring Complete Traceability and Compliance
In the complex domain of medical device software development, the assurance of traceability and compliance is fundamental. Utilizing an item-based approach, such as the one provided by Matrix Requirements, developers can achieve end-to-end traceability throughout the product realization process. This method ensures that every requirement, specification, test case, and risk assessment is interlinked and version-controlled, allowing for an effective evaluation of how changes in one area may impact another.
Moreover, this approach facilitates compliance with industry standards and regulatory requirements, including those stipulated by ISO 13485, MDR, and the FDA. By adopting integrated modules like MatrixALM for product-related documentation, each discrete piece of data—be it a requirement, risk, specification, or test result—is meticulously tracked and documented. What results is a cohesive documentation structure that not only aligns with the regulatory mandates but also enhances the efficiency and accuracy of the entire development process. With such a system, audits become more streamlined, and the path to market approval is clear and well-documented.
Linking Information Items for End-to-End Traceability
Achieving comprehensive traceability necessitates the contiguous linking of information items. This starts from product inception through design, development, validation, and post-market surveillance. The traceability ensures that the genesis and evolution of each information item are transparent and auditable.
When mapping out the product realization journey, a meticulous linkage of information items becomes imperative. This spans the complete lifecycle, linking requirements to design inputs, risk analyses to mitigation measures, and verification and validation activities to design outputs. By establishing these connections, the pathway of influence from one item to another becomes clear, facilitating impact assessments and promoting regulatory conformity.
Furthermore, the interconnection of information items using a tool like MatrixALM fosters a robust quality management system. It provides a clear lineage from the user need to the final product, including detailed change histories. This systematic tracking simplifies the process of identifying the repercussions of any modifications, ensuring consistent product quality and regulatory compliance.
The utility of an item-based approach is magnified when using tools such as Matrix Requirements' modules, MatrixQMS and MatrixALM. They provide an infrastructure where information items are inherently linked, ensuring that documentation is generated from a single source of truth. This centralised, dynamic repository of data facilitates a seamless transition through product approval stages, ensuring that no detail is overlooked and maintaining the integrity and availability of essential documentation.
Streamlining Reviews and Approvals with Matrix Requirements
In the intricate world of medical device software development, ensuring consistent and thorough document reviews and approvals can be daunting. However, with Matrix Requirements, this process transforms into an efficient and manageable workflow. This is achieved by leveraging an item-based approach for managing product realization documentation, where every information item is logged with changes, versioned, and linked for full traceability.
Matrix Requirements' sophisticated system automates the version control, allowing for real-time tracking of the documentation evolution. This ensures that reviewers are always looking at the current iterations of documents, thus avoiding the review of outdated materials.
Expedited feedback loops emerge thanks to configurable review phases within MatrixALM, which prioritize critical path items. This real-time insight into item statuses simplifies decision-making around when to initiate reviews and drive the approval process.
The integration of electronic signatures expedites the formal acceptance of documents. With features like electronic signatures, Matrix Requirements streamlines the validation of critical documents, aligning with regulatory requirements to ensure compliance with FDA and MDR regulations for electronic records.
Acknowledging the necessity for collaborative reviews, Matrix Requirements supports parallel reviews of information items. This invites diverse expert inputs which enhance the quality and compliance of the device software, mirroring the expectations placed upon medical device manufacturers by ISO 13485 standards.
Finally, Matrix Requirements adeptly facilitates the assembly of reports from approved items, crafting comprehensive documentation such as Product Requirement Specifications. The item-based approach guarantees that these reports are always up-to-date, accurately reflecting the current state of the product realisation lifecycle.